Could your Logistics Operations Benefit From the Introduction of Robotics?
- DC Space & Storage Solutions
- Nov 18, 2022
- 3 min read
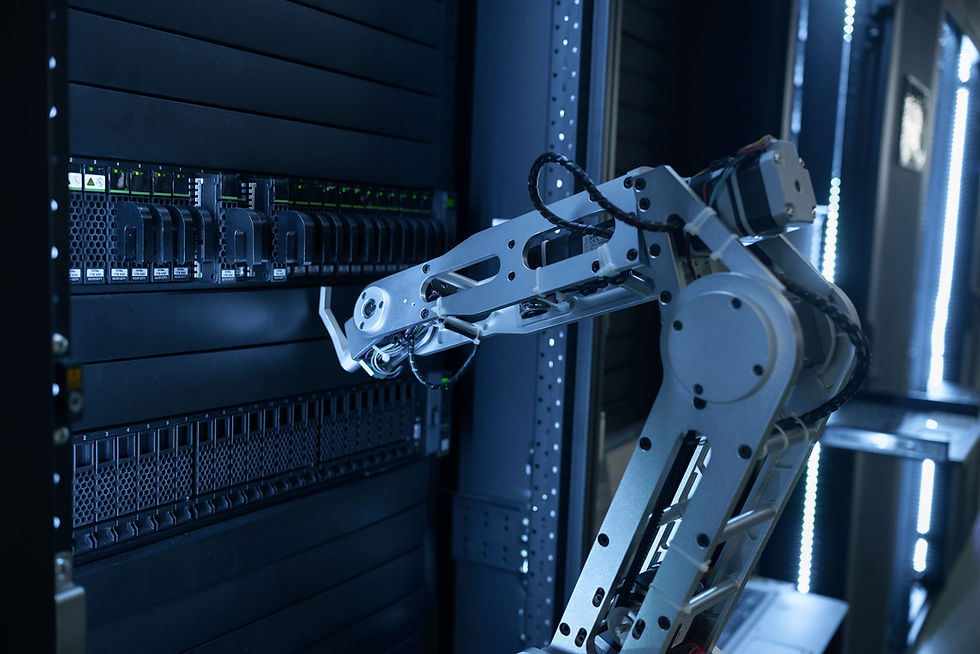
Have you been considering introducing robotics into your warehouse operations but you’re not sure whether it’s actually right for you? DC Space and Storage Solutions were recently invited onto a national discussion panel focusing on what exactly robotics are.
What are AGVs and AMRs?
An AGV is an Automated Guided Vehicle and AMR is an Autonomous Mobile Robot. AGVs use magnetic tapes with set points on to follow paths of preset guidance. AMRs are more dynamic machines programmed to navigate themselves to preset end points, they can navigate obstacles along the way.
What could cause problems when implementing these as solutions?
Automation requires good quantities of space, tidiness, and WiFi. Areas need to be available for the machines to work and they require flat, clean floors. There also needs to be effective WiFi to allow communication. If the warehouse floor is wet etc. it could cause robots to lose their bearings and create issues.
How do I know which is best for me?
Every area is different and there are multiple options for that very reason, so speak to an expert for personalised advice! As a simple guide, if your area is a fixed environment then AGVs may meet your needs effectively, but if there are more dynamic or changing areas then AMRs should be considered.
Why automation?
AGV and AMR are a rapidly growing area of change and should be embraced, particularly in regard to ‘non value added’ tasks. They can remove and automate tasks which don’t add an end value to the product, but also are repetitive tasks that human workers are not enthused about and cannot maintain constant speed at, e.g. moving pallets to dispatch. It works best where there is consistency of pallets, product sizing, packaging quality etc. as robots depend on the same boundary values every day. Automotive manufacturing is particularly suited to robots as it is repetitive tasks 24/7/365!
What should I do before investing?
Start getting good quality data. When starting out on this journey it’s very important to know flow numbers and locations etc to get the best value out of investments. If your data is no good, it can take extra time and planning at the installation phase.
How long does it take for systems to pay for themselves?
There are too many variables to offer a definite answer, but an average ROI is two years across a fleet of automation products. Experts are able to simulate automation and calculate ROI accurately for your specific circumstances.
What about my staff?
Repurpose your staff for value-added tasks where they can improve the value of the product. If they could be doing more valuable tasks then they should! Nobody needs to feel left out - learn to work in harmony with the provisions that do the tasks you hate. Robots can work piecemeal and can iron out peaks and troughs in your process including areas of space requirement and allocation. Start simply by introducing just a couple, and progress towards a fully automated solution.
Can these machines integrate with our existing Software?
Generally lots of software platforms can be linked directly but where there are issues you can consider the following solution.
Historic WMS - links to:
middle layer interface- links to:
Robotic layer
Are these Types of equipment safe?
AGV and AMR are safer than traditional MHE equipment. In fact they are intrinsically safe. If there is an issue then you will have a log, CCTV detail and hopefully an eye-witness of the event too. An incident with a robot is probably far safer than a forklift impact and 90% of racking collapses are actually caused by the forklift driver so you’re lessening this risk too.
Is there down time with these devices?
If you operate a fleet then creating overlap can ensure you remove downtime for maintenance and charging etc. AI is beginning to be used for preventative maintenance to ensure issues are highlighted and addressed before parts or machinery malfunctions.
How do I maintain such systems to realise their potential?
A set of PPMs (Path and Position Monitoring system) is critical, and cleanliness and tidiness are very important for their environment. All sensors should specifically be kept clean.
All in all these devices are getting smarter every day and are set to make huge inroads into the traditional way operating facilities are currently run. Want to know more? Talk to us @ DC Space & Storage Solutions Ltd about your project.
If you need help and research material then there is a good resource over at the BARA website with more information. (BARA - British Automation & Robot Association). https://www.ppma.co.uk/bara/about.html
Comments